Alpha Loop - multiphase flows in pipeline systems
Deltares’ Alpha Loop is a unique experimental facility for investigating a wide range of multiphase flows in pipeline systems. The Alpha Loop allows for single-phase (water), two-(phase) (water and air), and three-phase (water, air, and sediment) experiments. The Alpha Loop is applied with various clients and partners including industries, engineering firms, water authorities, and universities to assess design and operational questions.

The configuration allows for different geometries of pipes (length, slope, diameter etc) to be installed. This provides the opportunity to perform various types of tests in this system. Typical flow phenomena that can be investigated are:
- Slug flows in long inclined pipelines
- Solids re-entrainment in inclined pipes by air and water
- Acceleration of liquid slugs resulting from a gas blow out
- Rapid priming of pipelines
- Dynamic performance of pressure relief valves
- Performance and interaction of air valves
- Pigging & Flushing
- Leak detection
Deltares’ experts also use the Alpha Loop themselves for their own research programmes and software validation of the water hammer software package WANDA. As a result of the extensive validation by experiments, the WANDA package is a most reliable water hammer package for design and optimising operations of any hydraulic pipeline system.
You are invited to ask us any questions you may have about the safety, energy use, robustness or maintenance of your hydraulic pipeline system. Our experts will be happy to support you with specialist advice.
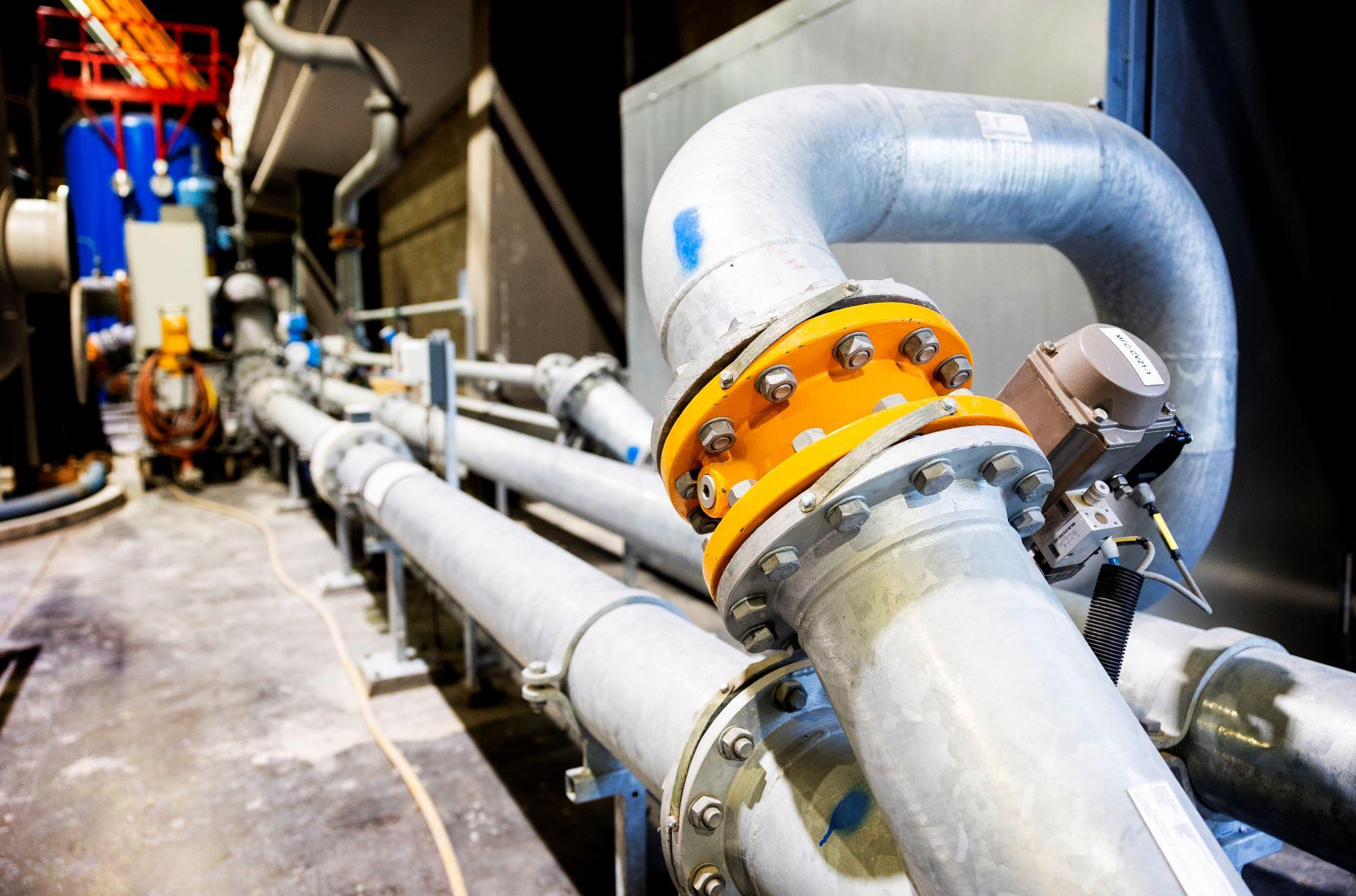
Alpha Loop facility description
The facility consists of a 320 m long pipeline loop, steel PN16 DN200; other diameters up to about 500 mm can be installed for assessment of scale effects. Transparent sections can be installed in various locations of interest in order to enable visual inspection of the flow patterns. A part of the loop is connected to a frame in order to enable the construction of arbitrary 2D pipe profiles (length-height). The frame has a length of 120 m and a height 7.5 m.
A crane is installed parallel to the flow loop in order to allow for simple and flexible construction of the specific loop design. The facility is equipped with two pumps. Each pump supplies water at a discharge ranging from 10 to 200 L/s at a pump head of about 50 m. The pumps can be arranged in series or parallel in order to provide additional head or flow rate capacity.
The air is supplied from a 70 m3 tank (PN16), which is filled by an air compressor. Optionally, an additional external compressor can be connected to the air tank for a supply up to about 3000 Nm3/h. If needed, a separator vessel (20 m3, PN16) can be used to separate the flow phases.
The intelligent design of the vessel’s internal lay-out allows for dedicated separation depending on the needs. The separator is connected to the air tank in order to pressurize the entire flow loop.
Instrumentation
Deltares has a wide variety of instrumentation available. Pressure can be measured at arbitarary locations of the loop using high performance pressure gauges. The flow rate is monitored using electromagnetic flowmeters and air vortex flowmeters. For challenging interface measurements, reliable instruments are installed.
Deltares has experience with a wide range of measurement techniques, such as optical and conductive void fraction measurements, accurate liquid level meters, Particle Image Velocimetry, Laser Doppler Anemonetry and Tomography.
We co-operate with Delft University of Technology for dedicated instrumentation. Instrumentation can also be custom made for a project. Deltares’ experienced instrumentation staff can design and build instruments to required specifications. Certain fluid properties, such as surface tension, can be measured and controlled during the experiments.
Applications
The test facility is designed such that a wide range of applications can be investigated, including:
- Multi-phase flow research for the oil & gas and water
- industry
- 2-phase and 3-phase flows in inclined pipe sections (to
- model terrain slugging in gas-condensate lines with or
- without sediment loading)
- 2-phase flow in downward sloping pipes, such as
- capacity reducing gas pockets
- 2-phase and 3-phase flows in very long horizontal pipe
- sections in order to establish flow patterns in large
- diameter pipes (in particular the slug flow regime)
- Collect validation data for multi-phase simulation
- software (in particular slug flow models)
- Component behaviour (air valves, separators, by-pass
- pigs, flow meters, pumps, process vessels) in 2- and
- 3-phase flows.
You have not yet indicated whether you want to accept or reject cookies. This means that this element cannot be displayed.
Or go directly to: